Underwear is one of the most essential clothing items, yet its simple design hides the complexities of manufacturing quality underwear at scale. While basic in function, manufacturing underwear at scale requires expertise in fabric selection, pattern design, process engineering and automation. Raw materials, proper patterns and precision machinery all come together to deliver quality underwear in bulk that meets buyer specifications. This article covers the basics of how underwear is made for wholesale suppliers, from materials and design to key manufacturing processes.
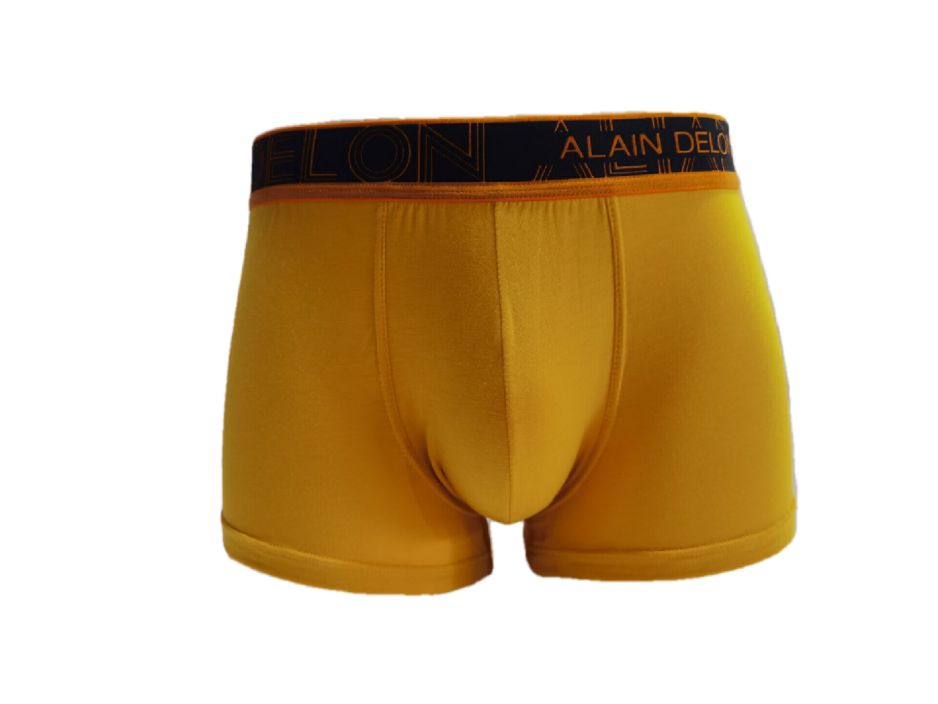
China nightwear manufacturer Tell You Materials Used in Underwear Manufacturing
Multiple materials go into making different types of underwear for both men and women:
- Cotton – The most common material used due to its comfort, breathability and absorbency. Available in different knit densities and weaves.
- Synthetic Fibers – Like polyester, nylon and spandex (elastane) provide better stretch, moisture management and quick-drying properties. Often blended with cotton.
- Lycra – A brand of spandex fiber that offers the highest elasticity, used for shapewear and compression underwear.
- MicroModal – An eco-friendly fabric made from beech tree fibers that is super soft and moisture-wicking.
- Lace – Used as a trim or all-over material for decorative women’s underwear. Can be made from cotton or synthetic fibers.
Different styles of underwear require specific fabric blends based on the properties needed. For example, sport underwear uses moisture-wicking fabrics while maternity underwear uses super stretchy fabrics.
Key Manufacturing Processes Through Nightwear China Manufacturer
Major processes involved in mass-producing underwear include:
- Cutting fabric according to patterns – Done using automatic cutting machines like laser cutters or plotters for high speed and precision.
- Joining waistbands and elastic strips to leg opening – Usually done using overlock sewing machines or ultrasonic welding.
- Stitching panels together – Seams are sewn using lockstitch machines to join front and back panels.
- Adding lace or other trims – Trims are sewn or bonded to underwear using specialized embroidery or welding machines.
- Packaging – Finished underwear sets are sorted, inspected and packaged using automated equipment.
- Quality control checks – Regular QC checks are done during inspection and testing to ensure comfort, sizing accuracy and defect removal.
Automation, particularly for cutting and sewing operations, helps large-scale underwear manufacturers achieve mass production capabilities. However, manual labor is still needed for tasks like elastic stripping, cropping loose threads and inspecting sew lines.
Underwear Design And Patternmaking
Professional patternmakers and designers create patterns or digitize designs that are used to cut fabric into various underwear components like waistbands, leg openings, front panels, back panels and more.
The patterns specify details like sewing allowances, grain directions and placement of components. Additional elements like elastic strips and lace trims are also specified in the design.